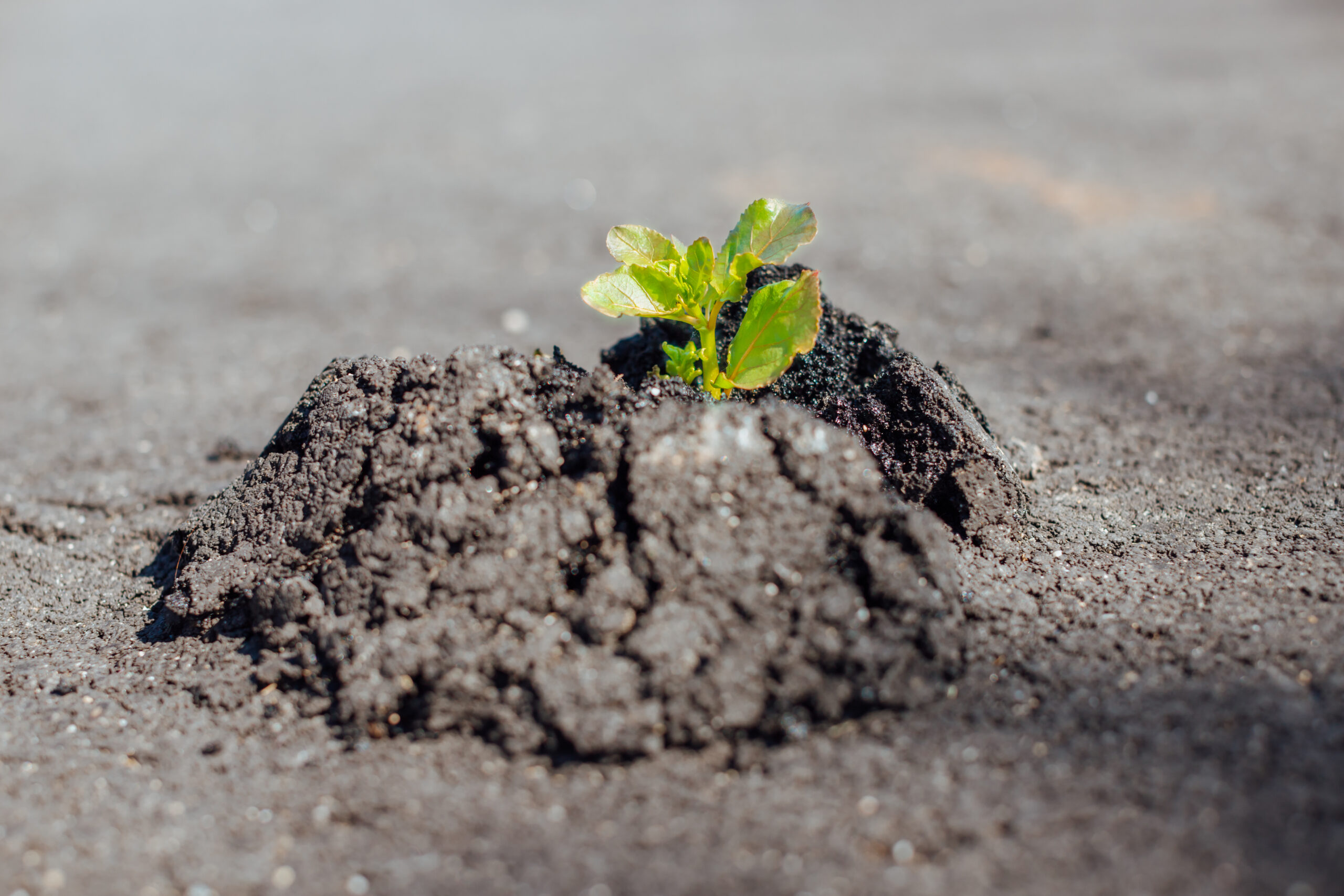
With mounting pressure from end users to reduce concrete’s carbon footprint, the entire industry is responding and looking for new strategies to reduce its relatively large footprint. These strategies can include new materials, technologies and processes to minimize carbon dioxide (CO2) emissions during production or approaches to actually absorb CO2 into the material. Let’s start by discussing the source of carbon emissions in the industry and then address some of the solutions.
Cement: An Ingredient in Concrete
The majority of concrete’s carbon footprint is actually attributed to CO2 produced during cement production. Cement acts as the glue that holds concrete products together. It is a critical ingredient. The production of one tonne of cement creates up to 0.8 tonne of CO2, making the carbon intensity of cement production the biggest environmental impediment for the concrete industry. There are two main sources of CO2 emissions associated with cement production:
- Fuel combustion – required to heat the raw materials of cement to high temperatures, and
- Calcination – CO2 is released during a chemical reaction that takes place during cement production.
For chemistry buffs, here is the science behind the reaction:
- When cement is produced, the raw material (limestone) is heated to produce lime (CaO), a precursor to cement – this reaction is known as calcination and releases a molecule of CO2 CaCO3 (limestone) → CaO (lime) and CO2
Cement production is ultimately responsible for about 5% of global carbon dioxide emissions. These emissions might not be a problem if there weren’t so much cement and concrete manufactured globally. According to the International Monetary Fund (IMF) database world economic outlook1, worldwide cement consumption reached a record estimated 3.6 billion tonnes in 2012. Future forecasts show that production will increase even higher owing to growing demand in developing markets. This also translates into increased demand for concrete. In fact, concrete is the world’s most widely used building material with about one tonne of concrete used per person every year.
The good news is that strategies are available to reduce the CO2 footprint of concrete masonry, grout and mortar. In fact, a recently published paper2 by Licht and colleagues in Chemical Communications entitled STEP cement: Solar Thermal Electrochemical Production of CaO without CO2 Emission3 hints of a future where cement can be produced with zero carbon emissions and therefore potentially yield carbon negative concrete products. This would be an important development for the industry and for the environment, given that cement and concrete production is on the rise.
Strategy to Reduce Carbon Intensity
Options are available today to make lower-carbon concrete products. Most of the efforts have been in developing lower-carbon cement, which in turn would yield concrete products with lower carbon footprints. The cement industry has three realistic avenues to reduce the carbon intensity (and thereby improve the sustainability profile of concrete):
- Thermal and electrical efficiency – Deploy best available technology in new cement plants (while pursuing retrofits where economically viable) to lower the energy requirements for producing cement
- Alternative fuels – Use less carbon-intensive fuels and/or alternate fuels to supply energy for cement production.
- Clinker substitution – Substitute clinker (a precursor to cement) with other low carbon materials with cementitious properties, for example fly ash or slag, byproducts of coal combustion and smelting or refining of ore, respectively.
To contextualize these efforts, currently clinker substitution can help achieve LEED points since it contributes to the recycled content credit of the Materials and Resources category. Other cement and concrete industry carbon intensity levers currently do not provide additional LEED points. Luckily, recently released LEED v4 rewards environmental efforts within the cement and concrete industry by issuing points for manufacturers who provide Environmental Product Declarations (EPDs). EPDs are tools used to measure the environmental impact of a product throughout its entire life cycle. Like nutritional labels, EPD documents communicate a building material’s environmental impact, transparently identifying ingredients and quantified data for preset categories.
Industry Transforming
There are several environmental advantages to using carbon-sequestering technology in the manufacturing process. Waste CO2 is added at an early stage of production – when the materials are being mixed. The CO2 gas is an accelerated curing agent. It induces a chemical reaction whereby cement undergoes carbonation to create limestone. It is converted into a solid – calcium carbonate – within the concrete. This means that CO2, which would have otherwise become a harmful greenhouse gas, now becomes safely and permanently embedded in the concrete.
The introduction of CO2 can also create other material advantages for the manufacturer, such as higher early strength of the concrete, as a result of the carbonation process. This higher early strength can translate into lower cement and energy requirements, reduced defects (solid waste) and other manufacturing benefits. The best part is that the products, which look and act like typical CMU, don’t have a significant cost premium – low-carbon products cost about the same as regular concrete products. The products also meet all required ASTM and CSA standards. The bottom line is that products made with carbon sequestering technology are green without the environmental or material tradeoffs.
Says Don Gordon, CEO of Atlas Block, “I have been in this industry many years, and this is easily the most exciting technological improvement I’ve seen. This process will be industry-transforming!” CarbonCure works with concrete products manufacturers to introduce its CO2-injecting technology into their plants. Currently it is working with several manufacturers to bring low-carbon concrete products to market. These forward-thinking companies include Shaw Group (Eastern Canada), Atlas Block (Ontario), Northfield (Illinois) and Basalite (Northern California). CarbonCure also engages with end users to encourage the adoption of green concrete in the market. Several architects, engineers and construction firms (AECs) have already specified low-carbon products for construction projects. (see sidebar) Designers are seeking sustainable products that meet all performance criteria. Some are now specifying low-carbon concrete masonry across all construction projects at their firms.
Leading the Challenge in Green Building Programs The building sector continues to push the limits on green, with the emergence of LEED v4, the Living Building Challenge and Architecture 2030. For instance, Architecture 2030 is challenging manufacturers to reduce their products’ carbon footprint by 50% by the year 2030. By combining several innovative approaches such as carbon sequestration technology, the concrete industry will be well positioned to meet the growing demand for low-carbon building materials.
Low-Carbon Concrete Masonry | SMART|dynamics of masonry
Above source: Robert Niven & Jennifer Wagner, LEED Green Associate written for Smart Dynamics of Masonry
Additional Resources
CMU Embodied Carbon: Not All Concrete is the Same | concrete-masonry-checkoff | CE Center
Lowering the Embodied Environmental Impacts of Cement and Concrete
Industry Average EPDs EPD_CMHA_v5.pdf
How Low-Carbon Concrete & Concrete Masonry Could Help Save the Planet